Non Ferrous
Carpenter Brothers, Inc. has a wide range of metals and alloys for non-ferrous applications. Whether you are melting aluminum, zinc, magnesium, copper, or brass, we have the metal additions you need. If you don’t see what you’re looking for, please send us an email or call to discuss your needs. There’s a good chance we either have it or can obtain it.
Metals Offered:
Aluminum Alloy Ingot
Antimony
Bismuth
Cobalt
Copper
Copper Alloy Ingot
Ferroaluminum
Iron Powdered Titanium
Magnesium – Butt Ends or Rods
Manganese
Nickel
Phosphorus Copper Rod or Shot
Silicon
Tin
Titanium
Zinc
Zirconium
Master Alloys:
- TiBor (Titanium Boron Aluminum)
- SrAl (Strontium Aluminum)
- Aluminum Manganese
- Aluminum Chrome
- Aluminum Boron
- Aluminum Nickel
- Aluminum Titanium
- Aluminum Copper
- Aluminum Magnesium
- Aluminum Zirconium
- Aluminum Silicon
- Aluminum Vanadium
- Aluminum Iron
- Aluminum Molybdenum
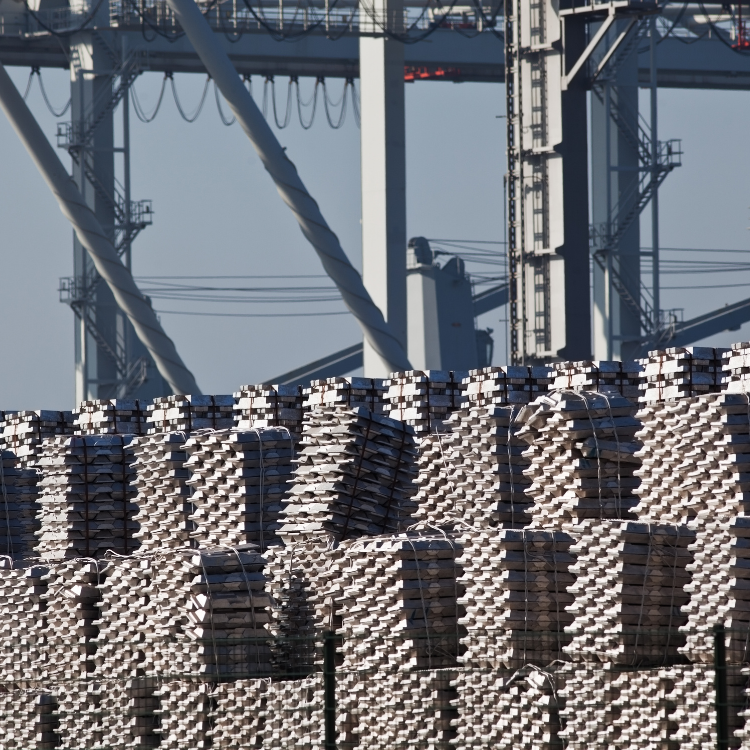
Non Ferrous Products
Carpenter Brothers, Inc. offers a complete line of foundry products to meet the requirements of the Metalcasting Industry.
Foundry Products
We supply the necessary foundry products you need to make a quality casting. Whether you need Metals & Alloys, Melting & Melt Quality, Molding & Core Making, Casting & Shakeout, Finishing & Surface Preparation, or Environmental Compliance products, we have what you need.
About Us
Carpenter Brothers, Inc. is the leading supplier of equipment, consumables, and technical expertise for the metal casting industry. Founded in 1917, by Everett and Milton Carpenter, the brothers were able to use their unique foundry experiences to solve the problem of the day: a reliable sand source. They got their foot in the door by selling natural bonded molding sand, which was mined by hand, loaded into horse-drawn carts, and then delivered to customers. Not only did they sell the sand, but their technical expertise was readily available for all customers, big or small, to help manufacture the best castings. After surviving The Great Depression, Carpenter Brothers, Inc. slowly increased the number of products it distributed and expanded its sales territory into what it is today.
Carpenter Brothers, Inc. has committed itself to its customer's success by providing exceptional service to go along with the superior products and equipment they supply. With multiple warehouses around the United States we can get you the products you need when you need them. Our logistics team can handle getting your order to you by truck, plane, or train. Our technical sales and engineering staff all have experience in the industry, so when you buy from Carpenter Brothers you gain access to all of our knowledge.