SphereOx Ceramic Foundry Sand®
SphereOx Ceramic Foundry Sand® has been specifically engineered for metal casters to provide the best performance in various castings. SphereOx Ceramic Foundry Sand® can be used to make molds and cores with almost every resin system, including phenolic urethanes, phenolic ester, furan, sodium silicate, bentonite clays/green sand, shell resins, and alkyd oils. It can also be used with virtually every metal you might be producing, including aluminum, gray iron, ductile iron, steel, copper, and magnesium.
SphereOx Ceramic Foundry Sand® outperforms specialty sands and, at the same time, offers distinct economic advantages. An additional process is used to melt the outside of the surface to provide an incredibly smooth, glass-like surface, allowing for lower resin usage with higher tensile strengths.
SphereOx Ceramic Foundry Sand®, versus silica sand, has a lower thermal expansion, resulting in higher precision and accuracy of castings while leading to lower scrap cost and lower cost to correct inaccuracies. In addition, its low thermal expansion and greater flow properties increase the ability to produce thin-wall, complex castings and minimize casting mass.
With lower density than other specialty media, SphereOx Ceramic Foundry Sand® requires less product (by weight) to produce an equal volume of cores or molds. As a result, it also provides a lower cost per cubic foot of product used. Also, the strength and durability of SphereOx CeramicFoundry Sand® enhance reclamation and reduces media consumption. SphereOx Ceramic Foundry Sand® is inert and contains no quartz silica.
SphereOx Ceramic Foundry Sand® reduces the occurrence of casting defects such as veining, penetration, and burn-on, resulting in lower cleaning costs. With a sphericity rating of almost 1, SphereOxCeramic Foundry Sand® enhances flow properties. The durability resists breakdown and media consumption while promoting reclamation lowering the cost associated with transportation, disposal, and replacement.
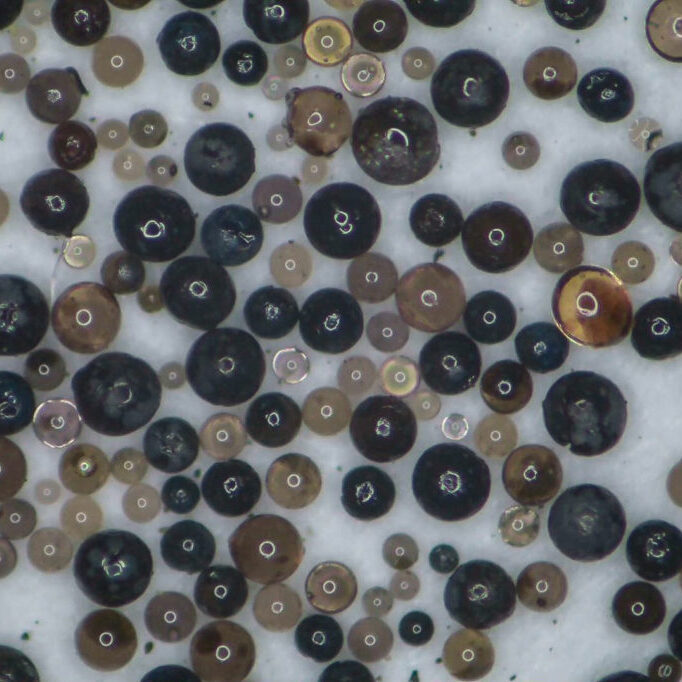
Chemical Analysis: Al2O3 – > 70%, SiO2 – 15-20%, Fe, Fe3O4, Fe2O3 – < 10%
Bulk Density: 115 lbs per cubic ft